Glenair - eVTOL Air Taxi & Advanced Air Mobility
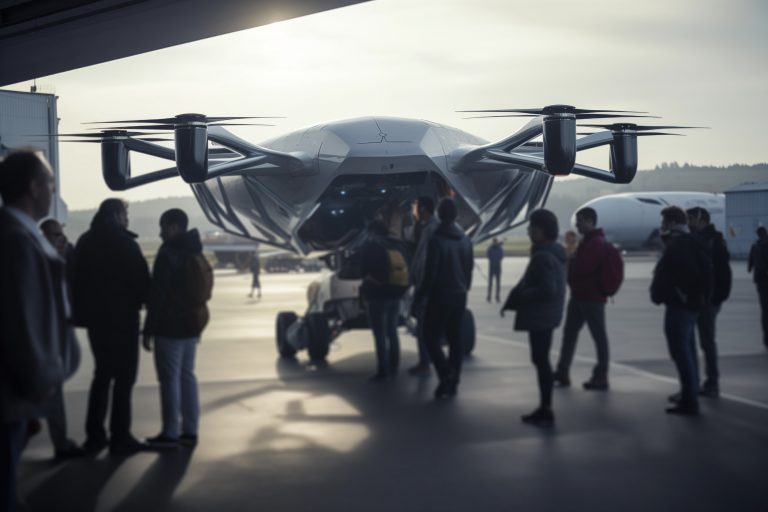
Glenair’s Signature Interconnect Technology for Advanced Air Mobility Aircraft Includes Connectors for Distributed Power Propulsion Systems, Avionics, Actuators, and Sensors.
Distributed Electric Propulsion (DEP) is a key element of all eVTOL aircraft. The native power sources in a DEP can be as simple as a single battery or as complex as a hybrid system made up of gas combustion engines, electric generators, fuel cells, and energy storage devices. Glenair manufactures a broad range of lightweight, rugged, aviation-grade power connectors and power feeder systems with proven commercial aerospace flight heritage. Glenair’s family of eVTOL air taxi interconnect solutions also includes high-density, small form-factor connectors for avionic systems, flight deck controls, actuators, and sensors. EWIS interconnect hardware for Urban Air Mobility includes lightweight composite thermoplastic backshells, EMC braided shielding, and lightning strike grounding systems.
Power Distribution Systems
- High-Current Connectors: For efficient and reliable power distribution to eVTOL propulsion systems.
- Bus Bars and Power Distribution Units: Ensuring stable and high-quality power supply throughout the aircraft.
Battery Management Systems (BMS)
- High-Density Connectors: For connecting battery modules and BMS components, supporting high power and data transmission needs.
- Shielded Cables and Assemblies: Providing EMI/RFI protection to ensure accurate monitoring and control of battery systems.
Flight Control Systems
- Lightweight, High-Speed Data Connectors: Essential for the avionics and flight control systems to manage real-time data transmission.
- Fiber Optic Solutions: Offering high bandwidth and immunity to electromagnetic interference, crucial for critical control data.
Propulsion Systems
- Heavy-Duty Circular Connectors: Designed to withstand the high vibrations and harsh conditions associated with electric propulsion systems.
- Environmental Sealing: Ensuring reliable operation in various environmental conditions.
Navigation and Communication Systems
- RF & Microwave Connectors: Supporting high-frequency communication systems for navigation, collision avoidance, and communication with ground control.
- Coaxial Connectors and Cable Assemblies: Ensuring signal integrity and reliability for navigation and communication equipment.
Sensor and Actuator Interfaces
- Miniature Connectors: Ideal for connecting sensors and actuators throughout the eVTOL, facilitating accurate data collection & system control.
- Ruggedized Solutions: Providing durability and reliability in demanding operating environments.
Cabin and Passenger Systems
- Multipin Connectors: For in-cabin systems, including lighting, environmental control, and passenger interfaces.
- Ethernet and Data Connectors: Ensuring high-speed data connectivity for infotainment and communication systems.
Autonomous and Remote-Control Systems
- Data Bus Systems: Enabling robust and high-speed communication for autonomous navigation and remote control operations.
- High-Reliability Connectors: Ensuring secure and dependable connections for critical autonomous system components.
Safety and Emergency Systems
- Redundant Connectors & Systems: Providing additional layers of safety through redundancy, ensuring continued operation in case of failure.
- Quick-Disconnect Solutions: Facilitating rapid and reliable disconnection in emergency situations.
Ground Support and Charging Infrastructure
- Heavy-Duty Power Connectors: For ground-based charging systems and infrastructure, ensuring efficient and safe power transfer.
- Durable and Flexible Cable Assemblies: Supporting various ground handling and maintenance operations.
Glenair’s interconnect solutions play a crucial role in enabling the reliable and efficient operation of eVTOL aircraft and address several challenges specific to electric vertical takeoff and landing (eVTOL) aircraft:
- Weight and Space Constraints – eVTOLs require lightweight components to maximize payload capacity and flight efficiency. Glenair’s interconnect solutions are designed to be lightweight and compact, reducing the overall weight and space requirements of electrical systems onboard
- High Power Requirements– eVTOLs rely on electric propulsion systems, which demand high power levels. Glenair’s interconnect solutions can handle high current and voltage requirements while maintaining reliability and efficiency, ensuring uninterrupted power delivery to critical components.
- Vibration and Shock Resistance– The rotor systems of eVTOLs generate significant vibration and shock during operation. Glenair’s interconnect solutions are engineered to withstand these harsh conditions, preventing electrical failures and ensuring continuous operation of essential systems.
- Environmental Protection– eVTOLs operate in various environmental conditions, including extreme temperatures, humidity, and exposure to moisture and chemicals. Glenair’s interconnect solutions offer robust sealing and protective coatings to safeguard against environmental factors, enhancing the longevity and reliability of electrical connections.
- Reliability and Durability– eVTOLs require components that can withstand frequent use and rigorous flight cycles. Glenair’s interconnect solutions undergo stringent testing and quality control measures to ensure reliability and durability under demanding operating conditions, minimizing downtime and maintenance costs.
- Electrical Power Propulsion System connectors, cables, and accessories
- Lightweight avionics, flight deck, actuator, and sensor connectors
- Wire and cable protection and management technology
- Shielding and grounding solutions for electromagnetic compatibility (EMC)
Featured Product Solutions
TurboFlex® Ultra-Flexible Power Distribution Cables are constructed from highly flexible conductors and high-performance insulation to produce cables ideally suited for applications where flexibility, durability, and weight reduction are required. Amazingly durable and flexible—especially in cold weather—the 16 AWG to 450 MCMTurboFlex cable features high strand-count rope-lay inner conductors made with tin-, nickel- and silver-plated copper. TurboFlex is jacketed with Glenair’s unique Duralectric™ compound that provides outstanding flexibility and resistance to environmental and chemical exposure. Duralectric is also low smoke, zero halogen. Long life and performance are critical in power distribution applications. TurboFlex, with its flexible conductors and durable jacket delivers both.
This multibranch TurboFlex power and data interconnect assembly for a ruggedized defense application demonstrates the remarkable flexibility and minimal bend radius of large form-factor (up to 450 MCM) TurboFlex cable. Example shown features UV- and chemical-resistant Duralectric jacketing in FED-STD 595C Safety Orange.
Turboflex wire is compatible with SuperNine PowerPlay Series, Series 80 Mighty Mouse, and Micro-Crimp PowerPlay Series, and Micro-D.
Features & Benefits:
- Ultra-flexible rope-lay power cable construction
- Turnkey high-voltage cable assemblies with Glenair signature connectors
- Broad range of gauges from 20 AWG to 450 MCM
- Low-smoke, zero halogen, and RoHS compliant
- Lightweight (L), radiation-resistant/low-temperature (K), jet fuel/chemical-resistant (F), and high-conductivity (C)
- High-performance Duralectric™ D jacketing standard
Duralectric™ is the high-performance TurboFlex® jacketing
material perfectly suited for immersion, chemical or caustic
fluid exposure, temperature extremes, UV radiation and more—
available in a broad range of colors including safety orange
Resources:
Series 806 Mil-Aero Micro Miniature D38999 Connectors and Cable Assemblies
Series 806 offers significant size and weight savings while meeting key performance benchmarks for a broad range of applications such as commercial and military aerospace, industrial robotics, transportation systems and more. Designed for general use in harsh vibration, shock and environmental settings — as well as high-altitude, unpressurized aircraft zones with aggressive voltage ratings and altitude immersion standards — the Series 806 Mil-Aero features numerous mechanical design innovations including durable mechanical insert retention, radial seals and triple-ripple grommet seals. Its reduced thread pitch and re-engineered ratchet prevent decoupling problems, particularly in small shell sizes, solving one of the major problems of shell size 9 and 11 MIL-DTL-38999 Series III connectors.
- Next-generation small form factor aerospace-grade circular connector IAW D38999
- Designed for general use in harsh application environments such as aircraft, industrial robotics and more
- Upgraded environmental, electrical and mechanical performance
- Integrated anti-decoupling technology
- Higher density 20HD and 22HD contact arrangements
- Glass hermetic, lightweight aluminum hermetic, high-temperature, fiber optic, and filtered versions
- High-Speed configurations with El Ochito octaxial contacts. Available turnkey factory terminated pigtail and jumper assemblies
The Series 806 Mil-Aero is an aerospace-grade micro miniature circular connector with triple-start threaded coupling. The 806 connector is smaller and lighter than conventional aerospace connectors. Featuring size 22HD, 20HD contacts plus size 8 power and high speed El Ochito®, quadrax, and fiber optic options. The Series 806 offers up to twice the number of contacts with no reduction in performance than MIL-DTL-38999 Series III. In fact, independent laboratory testing has demonstrated that the Series 806 meets, and in many cases exceeds, the requirements of MIL-DTL-38999.
But there is more to the 806 than just size and weight reduction. This flight-proven high-performance connector has many innovative features that meet the most aggressive requirements of the military/aerospace industry, including better resistance to vibration-induced decoupling. This is accomplished by re-engineering the ratchet mechanism and introducing a shallower mating thread ramp angle than is available in D38999.
Glenair pioneered integral shield banding platforms to allow direct attachment of cable shields, boots and overmolds. This innovation continues with the 806 — Glenair’s first connector to exclusively use the ultra lightweight Nano shield termination band for maximum size and weight reduction.
Another enhancement is a “top hat” insulator with raised bosses for foolproof alignment of insulator cavities and retention clips as well as higher voltage ratings.
The Series 806 Mil-Aero connector features an O-ring radial interface sealing design instead of a flat gasket. This allows for easier metal-to-metal coupling, improved sealing, and better EMI performance. The MIL-DTL-38999 Series III and other legacy aerospace circular connectors have a flat gasket inside the receptacle shell. This peripheral seal must be compressed sufficiently to allow full metal-tometal connector bottoming. In certain tolerance conditions this seal can make it difficult to fully mate the connectors “without the use of tools” as is required by MIL-DTL-38999.
Resources:
Learn More About “Mighty Mouse”
The Aircraft Industry’s most Advanced Power Distribution Interconnect with High-Current Carrying Capacity Crown Ring Contacts
PowerLoad™ is a high-vibration, high-temperature resistant connector series designed for aircraft power distribution in conventional, hybrid, and all-electric aerospace applications. An innovative combination of low-resistance contacts and a one-piece composite thermoplastic insulator—with aggressive contact cavity isolation—results in a reliable high-voltage (HV), high-current (HC), and high
frequency (HF) solution that optimizes wire-to-contact termination and weight reduction inpower distribution cables. Designed for use in integrateddrive generators, DC-to-AC inverters, electronic speed control applications (such as variable frequency (VFD) drive systems), PowerLoad is available in three- and six-contact layouts for both multiphase and high-frequency power designs. Removable wire-sealing grommet and wire separator allow for easy rear release of contacts and improved sealing of tape-wrapped wire.
Features & Benefits:
- The lightweight PowerLoad 28-6 layout connector is rated at 500 volts up to 50,000 ft. with a current of 45 amps per contact with 3 phase power in parallel at high frequency
- Available configurations include a high-vibration self-locking coupling nut plug, panel-mount receptacle with stub ACME mating threads, and bulkhead feed-thru for firewall applications
- Aluminum class connectors are rated to 200°C operating temperature; passivated stainless steel designs rated to 230°C
PowerLoad 972-101 Series
Plug with Banding Platform, Compression Grommet for Tape-Wrapped or Extrusion-Insulated Wire
- Socket towers for improved creep path performance
- Single-piece insulator eliminates bond lines that can lead to electrical failure
- High-vibration self-locking coupler
- High-temperature Crown Ring contact technology
- Patented wire sealing grommet
- Heavy-duty accessory interface
PowerLoad 972-102 Series
Wall-Mount Receptacle W/Branding Platform, Compression Grommet for Tape-Wrapped or Extrusion-Insulated Wire
Socket towers for improved creep path performance
Single-piece insulator eliminates bond lines that can lead to electrical failure
- High-temperature Crown Ring contact technology
- Patented wire sealing grommet
- Heavy-duty accessory interface
PowerLoad 972-103 Series
Jam-Nut Receptacle
Socket towers for improved creep path performance
Single-piece insulator eliminates bond lines that can lead to electrical failure
- High-temperature Crown Ring contact technology
- Patented wire sealing grommet
- Heavy-duty accessory interface
PowerLoad 972-203 Series
Feed-Thru Receptacle, Jam-Nut Mount
- Socket towers for improved creep path performance
- Single-piece insulator eliminates bond lines that can lead to electrical failure
- High-temperature Crown Ring contact technology
Crown Ring Crimp Pin Contact & Socket Contact
- Temperature rating: 260°C
- Contact resistance 40% of typical AS39029 contacts when mated to PowerLoad socket contacts
- Double-thick gold-plated on contact mating surfaces versus AS39029
- Passivated Stainless steel spring member on socket contact provides contact spring force and is resistant to stress relaxation up to 260°
The Power Connector for Extreme Environments – Series 970
Series 970 connectors fill the need for a military grade harsh environment power connector with improved mechanical, environmental and electrical performance. PowerTrip™ also delivers reduced size and weight compared to lower-density 5015 type power connectors. Featuring triple start mating threads, crimp rear-release contacts, upgraded finish choices and improved EMI protection, the PowerTrip™ connector is ideal for power distribution units, hybrid electric drives, motors, and other high current, high-reliability applications.
Features & Benefits:
- Fast, easy connector mating with triple-start ACME thread. 360° turn for full mating
- 5 polarizing keys, 6 keying positions
- LouverBand sockets for improved conductivity and longer life
- High conductivity copper alloy contacts
- Crimp, rear release contact system
- Splined backshell interface for improved EMI protection
- Ratcheting coupling for secure mating
- -65° C to +200° C
- Size 8, 4 and 1/0 contact sizes
- Last-mate, first-break size 12 and 16 contacts
SuperNine
Electrical Power Propulsion System Connectors, Cables, and Accessories. Series 973
SuperNine PowerPlay is a high-ampacity multi-pole connector series that combines the proven performance of MIL-DTL-38999 Series III connector packaging with contact and dielectric insert technology capable of 2000VAC working voltage. SuperNine PowerPlay utilizes Glenair Crown Ring contact technology, a crimp-removable, low insertion force contact series optimized for higher current carrying capabilities, lower contact resistance, and superior vibration resistance compared to LouverBand, hyperboloid, and other designs.
Features/Benefits:
- 2000 VAC working voltage
- High current, low resistance, superior vibration resistance
- Safe-touch finger proofing
- Integrated band platform shield termination
- Compatible with TurboFlex high-flexibility cable
- Support for busbar and other wire terminations
- Multi-Pin arrangements for size 8 and 4 AWG contacts. Single-Pole arrangements for 2, 1/0, 2/0, and 4/0 contacts. Options for 20 AWG interlock contacts on all sizes
Nowhere in the world does anyone supply such a complete range of high-performance backshells and connector accessories for mil-aero interconnect systems. Glenair is able to offer our SuperNine customers both military standard 85049 backshells and accessories, as well as unique special-purpose EMI/RFI and environmental backshells designed for higher performance requirements. This section of the SuperNine catalog presents just a few of our most innovative backshell designs, including our 3-in-1 Swing Arm™ strain relief, and several lightweight and corrosion-free composite thermoplastic solutions. Glenair’s high availability business model ensures all popular part numbers from this section of the catalog are in-stock and ready for immediate, same-day shipment.
Swing-Arm 3-in-1 Articulating Strain Relief
Glenair’s composite Swing-Arm® strain relief backshell is a lightweight and corrosion free cable clamp with cable shield termination options for a wide range of EWIS applications. This innovative backshell has become the standard shield termination device for weight reduction in both military and commercial airframe applications. Made from temperature-tolerant composite thermoplastic, rugged Swing-Arm® backshells offer easy installation, long-term performance, and outstanding weight and SKU reduction. Performance tested to stringent AS85049 mechanical and electrical
standards and available for all commonly-specified mil-standard and commercial cylindrical connectors includingMIL-DTL-38999, SuperNine, and Series 806Mil-Aero.
Features & Benefits:
- Significant weight reduction: no saddle bars or hardware
- Rapid assembly: cable self-centers on bundle, little or no wrapping tape required
- Braid sock and drop in band termination follower versions for EMI/RFI applications
- Internal conductive ground path
Integrated Shielding, Grounding, plus Band-Master ATS Braid Termination Solutions
Series 107
A single lightning strike can hit an aircraft with as much as 1,000,000 volts. Static electricity can charge an aircraft, particularly in cold and wet air, with enough electrical potential to result in a discharge that can ignite ground fueling equipment or fry avionics gear. Power generation systems (engines, alternators, starters, etc.) can also produce transient electrical current that can damage adjacent electronic systems.
Damage from these events is minimized and managed in aircraft, Navy ships, mass transit systems and elsewhere through the use of electrical bonding. Flexible bonding straps are attached between equipment and airframes as well as between structural elements and flight control surfaces to conduct destructive electrical surges to ground or to bus bar components capable of absorbing significant amounts of transient voltage
Glenair has designed and supplies a broad range of braided ground strap technologies to both commercial and military aerospace customers, as well as a broad range of mass transit applications. The ground strap technologies are exactingly designed with appropriate conductive and dissipative materials for each application. Click the Image to View Glenair’s Shielding/Grounding Solutions E-Book.
Included in this product group is: Swing-Arm 3-in-1 Backshells with integrated Shield Socks, Braided Ground Straps, Piggyback Boots, Band-Master ATS, Heat Shrink Termination Sleeves
Features & Benefits
- Ultra-lightweight EMI/RFI braided sleeving for EMC and lightning strike applications
- Best performing metallic braid during lightning tests (IAW ANSI/EIA-364 75-1997Waveform 5B)
- Microfilament stainless steel: 70% lighter than NiCu A-A-59569/QQB575
- Outstanding EMI/RFI shielding and conductivity
- ArmorLite™ CF with enhanced corrosion protection
- Superior flexibility and “windowing” resistance: 90 to 95% optical coverage
- 70,000 psi (min.) tensile strength
Braided Ground Straps Selection Guide