OIL & GAS
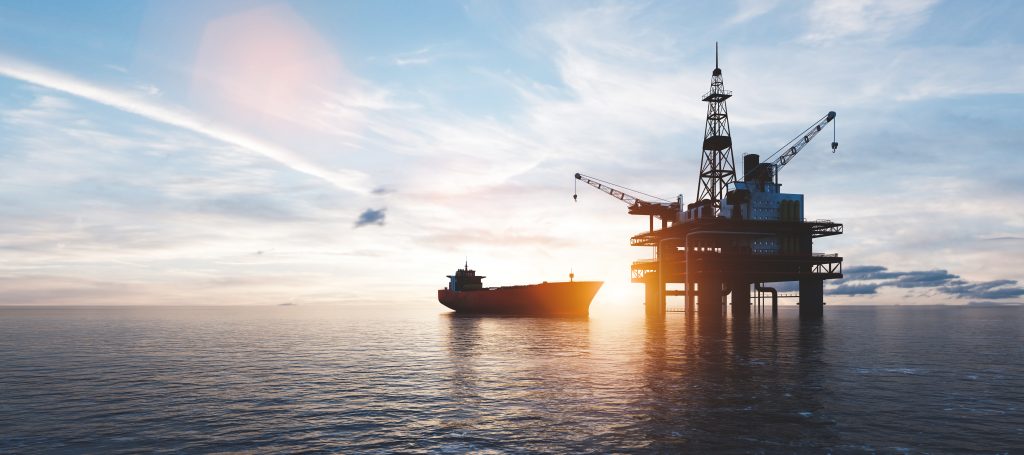
Glenair offers a full-spectrum of product lines designed to meet every interconnect requirement, including a broad range of military qualified and commercial connectors for the Oil & Gas industry.
Glenair excels in underwater connectors, custom high-pressure cable, Pressure Balanced Oil Filled (PBOF) assemblies, and connector terminations depth-rated to 10,000 psi (700 BAR) for naval and defense, deep-sea oil and gas industry, pipeline inspection (PIG), and oceanographic applications. Also, downhole, high-pressure and above-deck shipboard interconnect solutions. Underwater dry-mate fiber optic and high-speed digital solutions with 10KPSI pressure ratings.
Applications, Challenges, Solutions
Harsh Environmental Conditions: Oil and gas operations often take place in extreme environments, including offshore platforms, desert regions, and Arctic climates. Glenair’s connectors and cable assemblies are designed to withstand such harsh conditions, offering ruggedness, reliability, and resistance to temperature extremes, moisture, and corrosive substances.
Reliability and Durability: In critical applications like drilling, production, and refining, equipment reliability is crucial. Glenair’s interconnect solutions are engineered for high reliability, ensuring continuous operation even in challenging conditions. By providing robust connections, Glenair’s products contribute to minimizing downtime and enhancing operational efficiency.
Data Communication and Control: Modern oil and gas operations rely heavily on data acquisition, monitoring, and control systems. Glenair’s connectors and cable assemblies play a vital role in facilitating secure and efficient data transmission between various equipment components, sensors, and control systems. This helps improve operational safety, optimize processes, and ensure compliance with regulatory requirements.
Safety and Compliance: The oil and gas industry operates within a stringent regulatory framework, with strict safety and environmental standards. Glenair’s products adhere to industry standards and certifications, ensuring compliance with safety regulations and reliability in demanding applications. By providing dependable interconnect solutions, Glenair helps oil and gas companies meet regulatory requirements and maintain safe operations.
Maintenance and Serviceability: Oil and gas equipment often requires regular maintenance and occasional repairs, which can be challenging in remote or inaccessible locations. Glenair’s products are designed for easy installation, inspection, and maintenance, helping to minimize downtime and reduce the overall cost of ownership for oil and gas operators.
Dry-Mate, Subsea, Wet-Mate, Pipeline, Topside Connectors and PBOF Assemblies for High-Pressure Oil & Gas Industry Interconnect Applications
High-performance, high-pressure interconnect technologies with proven sealing performance in shipboard, downhole, and underwater applications.
> High Pressure, 10K PSI Open-Face Subsea
> Ruggedized Serial and High-Speed Electrical Connectors
> Power and Fiber Optic Interconnects
> Hazardous Zone ATEx Explosion-Proof
> Ultra High-Density Solutions for ROVs
Featured Product Solutions:
Microminiature high-pressure connectors and cables
The Series 707 Micro-PSI is an ultra-miniaturized 10K PSI high-pressure, high-temperature interconnect designed specifically for pipeline inspection applications in Magnetic Flux Leakage and ultrasonic pipeline inspection PIGs. The Micro-PSI insert arrangements feature two high-density micro TwistPin layouts for sensor applications and high-speed Gigabit Ethernet, and a Coax contact layout for 5 GHz performance.
Micro-PSI connectors are supplied as discrete plugs, or overmolded plug cordsets with rugged Viton or Polyurethane jacketing. Bulkhead and flange mount receptacles are 10K psi open-face pressure sealed, and incorporate fused vitreous glass inserts for <1×10-7 scc He/sec hermetic performance. Serviceable O-rings on plugs and dual piston and face O-rings on receptacles provide high-reliability sealing.
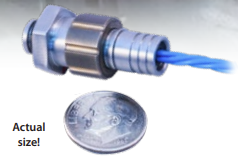
Features
- 10,000 PSI Pressure Rated
- 5 GHz Coax
- Temperature range -20° to +150°C
- High Density, small form factor
Benefits
Series 707 Micro-PSI affords PIG designers the opportunity to design out legacy large form-factor connectors with a dramatically smaller interconnect solutions.
Compact Design, High Pressure Resistance, Rugged Construction, Hermetic Sealing, Versatile Configurations, Compatibility with Sensors, & Compliance and Certification
When precision and reliability are critical, Micro-PSI connectors deliver unparalleled performance. With their miniature size and high-pressure sealing capabilities, these connectors are ideal for downhole tools, sensors, and instrumentation in oil and gas exploration and production. Experience exceptional signal integrity and durability with Micro-PSI connectors.
Resources:
ITS-Ex: IECEx/ATEX Qualified, UL Certified Hazardous Zone Connectors
Glenair is a qualified manufacturer of connectors for potential explosive zone use, built IAW IECEx/ATEX standards. The connectors may be used in application areas where flammable gases and vapors are present as a normal condition of operation (group IIC) and with temperature classes T6 and T5, zones 1 and 2; and for applications where potentially flammable dust is present as a normal condition of operation (group IIIC) and with temperature classes T80°C and T95°C in zone 21 and 22. The connector series design is optimized for fast and easy crimp-contact wire termination with ample wiring space in the cable housing and accessory hardware.
Features
- Over 40 power and signal contact arrangement
- Full support for common armored and unarmored cable types
- MIL-DTL-5015 crimp-contact derivative solution
- Locking set screw-equipped coupling nut and protective safety covers
- Extended shell labyrinth cooling zone and potting chamber features
- Mechanical cable clamp, basket weave, and Ex d cable gland accessories
- IP68 water, vapor, moisture and dust protection in mated condition
Well-Master™ 260° High-Temperature Micro-D Connectors
Oil, gas and geothermal wells can expose electronic equipment to temperatures in excess of 200°, exceeding the recommended operating temperature of standard Micro-D Connectors. For these demanding environments Glenair has developed the Well-Master™ to provide continous operation in temperatures of 260° or more. With key features such as rugged Passivated Stainless steel shells and hardware, hightemperature liquid crystal polymer (LCP) insulators allow these connectors to survive the most demanding high-termperature environments.
Features
High-Temperature Operation: The Well-Master 260 C Micro-D connectors are designed to withstand high temperatures encountered in downhole environments, up to 260°C (500°F). This feature ensures reliable performance and continuity of electrical connections in extreme heat conditions.
Rugged Construction: These connectors are built with rugged materials and construction methods to withstand harsh downhole conditions, including high pressure, vibration, shock, and exposure to corrosive fluids and gases. Their robust design ensures durability and long-term reliability in demanding oil and gas applications.
Hermetic Sealing: The connectors feature hermetic sealing options, providing an extra layer of protection against moisture, gases, and contaminants. Hermetic sealing helps maintain the integrity of electrical connections, preventing corrosion and ensuring reliable performance in challenging downhole environments.
Compact Size: The Micro-D form factor of the Well-Master 260 C connectors allows for high-density packaging in downhole tools and equipment. Their compact size enables space-saving designs and facilitates integration into small and confined spaces commonly encountered in downhole drilling and production operations.
Customizable Configurations: Glenair offers customizable configurations for the Well-Master 260 C Micro-D connectors to meet specific application requirements. This includes options for different contact layouts, termination styles, and materials, allowing for tailored solutions based on the needs of downhole operations.
High Electrical Performance: These connectors provide high electrical performance, including low contact resistance and high insulation resistance, ensuring efficient signal transmission and data integrity in downhole applications. They are engineered to meet the stringent requirements of the oil and gas industry for reliable electrical connections in critical downhole equipment.
Compliance and Certification: The Well-Master 260 C Micro-D connectors comply with industry standards and certifications relevant to downhole applications in the oil and gas sector. This ensures compatibility and reliability in regulatory-compliant installations, providing assurance to operators that the connectors meet stringent quality and safety requirements
Benefits
- Reliable Electrical Connections
- High Temperature Resistance
- Corrosion Resistance
- Hermetic Sealing Options
- Customizable Configurations
- Compliance and Certification
High-density, dry-mate, harsh-environment connectors and cables for lighter-duty ROV applications
High-density Series 701 SeaKing Junior connectors are the perfect choice for harsh-environment oil & gas industry equipment. All designs are equipped with single piston seal nitrile O-rings to withstand exposure to corrosive chemicals and high-pressure environments. These 5000 PSI pressure rated (mated condition, shell size dependent) connectors feature high-density crimp-contact or solder cup inserts, and are significantly smaller than our larger form-factor heavy-duty series 700 SeaKing interconnects. Gold-plated crimp contacts accept #12–30 gage wire. SeaKing Junior connectors are backfilled with epoxy potting compound, ready for easy incorporation into overmolded cables. Crimp-contact versions for field installation and repair are also available. SeaKing Junior is
specifically designed for high-pressure, mated condition applications that do not require the extra fail-safe features and cost of an open-face rated solution.
Features
- 5000 PSI (mated condition) pressure rated connector for overmolded (non-PBOF) applications
- High density, small form-factor solution—up to 50% reduction in size and weight compared to industry standard solutions
- Ultraminiature high-density pin configurations: #22D, #20, #20HD, #16, #12, #8 signal, power, fiber optic and high-speed datalink shielded contacts
Benefits
- Subsea Compatibility: Seaking Junior connectors are specifically designed for use in subsea environments, making them well-suited for oil and gas applications that require underwater connectivity. They can withstand the challenges posed by high pressures, corrosive seawater, and extreme temperatures encountered in subsea drilling, production, and exploration activities.
- Rugged Construction: These connectors are built to withstand harsh environmental conditions, including immersion in seawater, vibration, shock, and mechanical stress. Their robust construction ensures reliability and durability in challenging offshore environments, minimizing the risk of connector failure and downtime.
- Hermetic Sealing: Seaking Junior connectors often feature hermetic sealing options, which provide an extra layer of protection against moisture and other contaminants. Hermetic sealing helps maintain the integrity of electrical connections in subsea applications, preventing corrosion and ensuring long-term reliability.
- High Performance: Seaking Junior connectors offer high electrical performance, ensuring reliable signal transmission and data integrity in demanding subsea applications. They provide low contact resistance and high insulation resistance, enabling accurate data acquisition and control in critical offshore operations.
- Modular Design: These connectors typically feature a modular design, allowing for easy installation, maintenance, and repair in subsea equipment and systems. Modular components can be quickly replaced or upgraded as needed, minimizing downtime and reducing overall operating costs for oil and gas operators.
- Versatile Configurations: Glenair offers Seaking Junior connectors in various configurations to meet specific application requirements. This includes options for different contact layouts, termination styles, and materials, allowing for customization based on the needs of the oil and gas industry.
- Compliance and Certification: Seaking Junior connectors comply with industry standards and certifications relevant to subsea applications in the oil and gas sector. This ensures compatibility and reliability in regulatory-compliant installations, providing assurance to operators that the connectors meet stringent quality and safety requirements.
TurboFlex® Ultra-Flexible Power Distribution Cables are constructed from highly flexible conductors and high-performance insulation to produce cables ideally suited for applications where flexibility, durability, and weight reduction are required. Amazingly durable and flexible—especially in cold weather—the 16 AWG to 450 MCMTurboFlex cable features high strand-count rope-lay inner conductors made with tin-, nickel- and silver-plated copper. TurboFlex is jacketed with Glenair’s unique Duralectric™ compound that provides outstanding flexibility and resistance to environmental and chemical exposure. Duralectric is also low smoke, zero halogen. Long life and performance are critical in power distribution applications. TurboFlex, with its flexible conductors and durable jacket delivers both.
This multibranch TurboFlex power and data interconnect assembly for a ruggedized defense application demonstrates the remarkable flexibility and minimal bend radius of large form-factor (up to 450 MCM) TurboFlex cable. Example shown features UV- and chemical-resistant Duralectric jacketing in FED-STD 595C Safety Orange.
Features & Benefits:
- Ultra-flexible rope-lay power cable construction
- Turnkey high-voltage cable assemblies with Glenair signature connectors
- Broad range of gauges from 20 AWG to 450 MCM
- Low-smoke, zero halogen, and RoHS compliant
- Lightweight (L), radiation-resistant/low-temperature (K), jet fuel/chemical-resistant (F), and high-conductivity (C)
- High-performance Duralectric™ D jacketing standard
Duralectric™ is the high-performance TurboFlex® jacketing
material perfectly suited for immersion, chemical or caustic
fluid exposure, temperature extremes, UV radiation and more—
available in a broad range of colors including safety orange
Resources:
TurboFlex® Ultra-Flexible Power Distribution Cables are constructed from highly flexible conductors and high-performance insulation to produce cables ideally suited for applications where flexibility, durability, and weight reduction are required. Amazingly durable and flexible, especially in cold weather, the 16 AWG to 450 MCM TurboFlex cable features high strand-count rope-lay inner conductors made with tin-nickel- and silver-plated copper. TurboFlex is jacketed with Glenair’s unique Duralectric™ compound that provides outstanding flexibility and resistance to environmental and chemical exposure. Duralectric is also low smoke, zero halogen. Long life and performance are critical in power distribution applications. TurboFlex, with its flexible conductors and durable jacket delivers both.
This multibranch TurboFlex power and data interconnect assembly for a ruggedized defense application demonstrates the remarkable flexibilityand minimal bend radius of large form-factor (up to 450 MCM) TurboFlex cable. Example shown features UV- and chemical-resistant Duralectric jacketing in FED-STD 595C Safety Orange.
Turboflex wire is compatible with SuperNine PowerPlay Series, Series 80 Mighty Mouse, and Micro-Crimp PowerPlay Series, and Micro-D.
Features & Benefits:
- Ultra-flexible rope-lay power cable construction
- Turnkey high-voltage cable assemblies with Glenair signature connectors
- Broad range of gauges from 20 AWG to 450 MCM
- Low-smoke, zero halogen, and RoHS compliant
- Lightweight (L), radiation-resistant/low-temperature (K), jet fuel/chemical-resistant (F), and high-conductivity (C)
- High-performance Duralectric™ D jacketing standard
Duralectric™ is the high-performance TurboFlex® jacketing
material perfectly suited for immersion, chemical or caustic
fluid exposure, temperature extremes, UV radiation and more—
available in a broad range of colors including safety orange
Resources:
MIL-STAR Cable
NAVSEA S9320-AM-Pro-020/MLDG REV3 Certified Harsh-Environment Hookup Wire for PBOF and Wire Harness Assemblies
SpeedLine High-Speed Protocol Cables
Glenair supplies a wide range of high-speed shielded twisted pair cabling for use with El Ochito®, VersaLink™, SpeedMaster™, and other
of our shielded high-speed connector and contact technologies. High flexibility and high-density reduced-weight cable designs are a
specialty. Glenair offers turnkey Cat 8 Ethernet, SuperSpeed USB 3.0, HDMI, SATA, and other solutions for rugged application environments
including high-pressure subsea. Glenair SpeedLine cables are optimized for signal integrity, weight savings, flexibility, and durability. In addition, these harsh-environment cables have been optimized for ease of termination and across-the board compatibility with our broad range of high-speed contact modules and connectors.
Features & Benefits:
- Cat 8 Ethernet, SuperSpeed USB 3.0, HDMI, SATA, and other solutions for mission-critical applications
- Individual foil shielding around each data pair for reduced crosstalk and attenuation
- Up to 200°C high-temperature-rated cable
- RoHS compliant versions
- Ethernet versions meet ANSI/TIA 568-C.2 Category 6A requirement up to 262 feet/80 meters
- Low-skew SuperSpeed USB data pairs have individual braided shields
- Water- and pressure-resistant jacketing and overmolding materials
FIBERKING Fiber Optic Cables
Glenair FiberKing fiber optic cables are optimized for reliable, durable performance in military and commercial aviation,
space, harsh-environment oil and gas, and multi termination (MT ribbon) assemblies.
Features & Benefits:
- Lightweight, tight bend-radius fiber optic cable for 10Gb+ avionic networks
- Vibration, radiation, and temperature-resistant space-grade F/O designs
- Ultra harsh-environment (high-pressure, high temp, water-blocking) oil & gas industry fiber optic cable assemblies
- Ruggedized fiber optic ribbon cable for multi fiber termination (MT) applications
BLUMARK RF Coax Cables
BluMark RF 50 Ohm Coax Cables are available in seven size categories. These high-frequency, low-loss, flexible cables are
suitable for radar and other aerospace applications as well as laboratory test equipment. Jacket options include FEP and
radiation-resistant space-grade ETFE. Triple-shielded high performance cables have expanded PTFE dielectric core for
low loss up to 40 GHz. Application selection is based on compatibility with a particular RF / microwave connector type
and size, as well as flexibility, EMI screening, weight considerations, temperature tolerance, and altitude.
Request a Quote